Choosing the right dual shaft shredder involves considering several key factors to ensure that the equipment meets your specific needs and provides the best cost-benefit ratio. Here’s a comprehensive guide to help you make an informed decision:
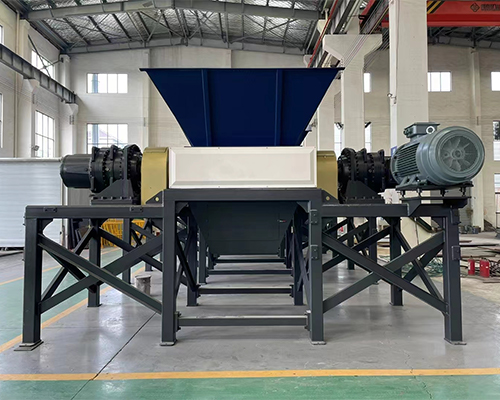
1. Material Type and Characteristics
- Material Type: Identify the primary materials you will be processing, such as scrap metal, plastic, wood, paper, etc. Different materials may require different types of blades and shredding methods.
- Material Hardness: Assess the hardness of the materials. Harder materials may need more robust blades and higher torque.
- Material Size and Shape: Determine the maximum size and shape of the materials to ensure the chosen shredder can handle them effectively.
2. Throughput Capacity
- Daily Processing Volume: Estimate the total amount of material you need to process daily. Choose a shredder with a capacity that meets or slightly exceeds this demand to handle peak times efficiently.
- Continuous Operation: Consider whether the shredder will need to operate continuously for long periods. If so, opt for a model with high reliability and durability.
3. Equipment Specifications
- Inlet Size: Ensure the shredder’s inlet size can accommodate your largest pieces of material.
- Output Particle Size: Determine the desired particle size of the shredded material. Some applications may require finer particles, while others can handle larger pieces.
- Motor Power: Select a motor power that matches your throughput and material hardness requirements to ensure efficient operation.
4. Technical Parameters
- Blade Material: High-quality blade materials, such as high-strength alloy steel, enhance durability and shredding efficiency.
- Number and Configuration of Blades: More blades and optimal configuration improve shredding performance and uniformity.
- Reducer Type: Choose the appropriate type of reducer (e.g., planetary, hard-toothed) to ensure smooth and energy-efficient operation.
5. Safety and Reliability
- Safety Features: Ensure the shredder has essential safety features such as emergency stop buttons, safety interlocks, and overload protection.
- Maintenance Accessibility: Select a shredder that is easy to maintain and clean to minimize downtime and maintenance costs.
- Brand and After-Sales Service: Opt for well-known brands that offer reliable technical support and after-sales service.
6. Cost-Benefit Analysis
- Initial Investment: Compare the prices of different brands and models to find the best value for money.
- Operating Costs: Consider ongoing costs such as energy consumption, maintenance, and blade replacement frequency.
- Return on Investment: Evaluate the economic benefits the shredder will bring, such as increased production efficiency and reduced labor costs.
7. Compliance and Standards
- Regulatory Compliance: Ensure the shredder meets local safety and environmental regulations.
- Certifications: Choose shredders that have international certifications like ISO to guarantee quality and performance.
8. User Reviews and Case Studies
- Customer Feedback: Read reviews and feedback from other users to understand real-world performance.
- Case Studies: Examine case studies from similar businesses to gain practical insights and success stories.
Practical Steps
- Consult Professionals: Engage with equipment suppliers or industry experts to get professional advice.
- Site Visits: Visit the supplier’s manufacturing facility or customer sites to see the equipment in action.
- Trial Period: If possible, request a trial period to test the shredder and verify its suitability for your needs.
By following these steps and considerations, you can select a dual shaft shredder that is well-suited to your specific needs and provides long-term value and efficiency.
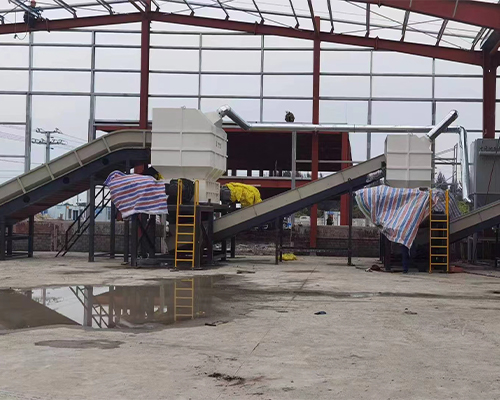
Model | 600 | 800 | 1000 | 1200 | 1400 | 1600 | 1800 |
Motor(kw) | 11*2
| 18.5*2 | 35*2 | 45*2 | 55*2 | 75*2 | 110*2 |
Reducer | P6-P7 | P7-P8 | P8-P10 | P10-P12 | P11-P13 | P12-P16 | P14-P16 |
Siemens or other motors, planetary reducers or other reducers can be customized according to customer requirements |
Rotation Speed | 8-20rmp
| 8-20rmp | 8-15rmp | 8-15rmp | 8-15rmp | 8-12rmp | 8-12rmp |
Blades Diameter | 220-320 | 260-320 | 260-400 | 400-500 | 400-500 | 500 | 500 |
Blades material | The material of the blades (55sicr, 5crsi, 9crsi, skd11, m6v, h13) can be customizedaccording to the customer's actual usage |
Feeding Size | 1200*900mm | 1400*1000mm | 1600*1200mm | 1800*1300mm | 2000*1300mm | 2200*1700mm | 2400*2000mm |
The size and appearance of the feeding hopper can be customized according to thecustomer's feeding situation |
Weight(kg) | 1800
| 2500 | 3700 | 5500 | 7500 | 9500 | 13000 |
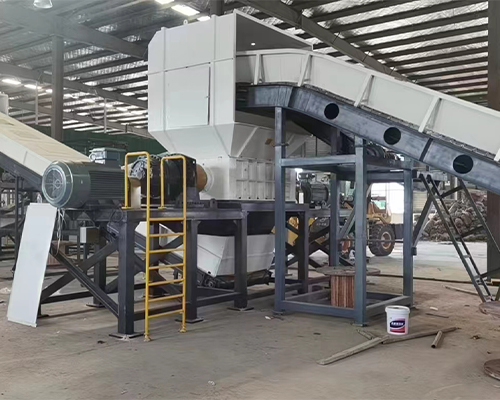